First published in Food & Drink Business Online
Wiley senior process engineer Scott Hebbard explores the energy issue, and how to manage it.
The rising cost of energy is a hot topic.
This pressure on Australia’s food processing industry and the market again brings the focus on reining in the cost of powering operations.
In food production and the supply chain, the energy demands mean this is always one of the largest burdens.
Rising energy costs loom large across the industry and operations are looking for new or alternative ways to solve their energy issues, especially in the current climate of retail price escalation and anticipated continued cost growth for the next decade.
When it comes to solutions or mitigation strategies for energy costs, there are three main options relevant to the food processing industry. We can reduce our energy consumption, produce our own energy or manage our energy.
Reduce consumption
Reducing power consumption is a business problem, not just an engineering problem and must be addressed strategically with appropriate detailed knowledge of the available options.
In truth, there are always more energy efficient ways to operate a food manufacturing business; the trick is in spotting the point of diminishing returns.
Start with an audit of your operation and understand the detail and profile of your power consumption.
Find out when it spikes, what causes the biggest drain, what can be reduced, and the baseline that is simply the cost of doing business.
Importantly, there may be more contemporary means of processing that are more energy efficient.
For instance, the reduction in power consumption of replacing an aging piece of plant could reduce operational costs enough to offset the capital cost of the new plant over its lifecycle, making the decision cash flow positive.
Once you have audited your facility, you will be able to see where your energy is going. Is there an opportunity to move a step in your operation to a cheaper time?
You may be able to save greatly on power by moving your processing or refrigeration steps to an earlier or later time.
From the audit there is also the opportunity to assess and potentially change your energy source, be it from supplied energy or produced energy.
In food production, refrigeration can account for up to 85 per cent of energy costs, so improving the efficiency of refrigeration plant can help reduce energy costs.
To improve your energy efficiency in refrigeration you might investigate the lower hanging fruit such as rapid roll doors, draft isolation, better insulation or energy efficient facility design, optimised policy on staff movements, load in and load out, access to the cold store.
Once the low hanging fruit has been picked, consider operational improvements uch as implementing variable control, optimising plant location and control automation.
Logistics automation for transporting product can save costs because shuttles and AGVs access cold stores efficiently and don’t make multiple trips because they forgot something.
Autonomous units have other potential ways to save costs as they are also safer than people and the only thing more costly than a huge power bill is a coroner’s inquest.
Lighting is another area where there is often a large degree of inefficiency and unnecessary long term costs that are not reviewed regularly.
The good news is that there are technologies available such as LED lighting and control system that are being developed all the time to improve efficiencies in food processing facilities.
Significant savings are often realised through the elimination of waste and leaks in such services as steam, condensate return and compressed air.
By reducing your energy requirements, you will reduce costs as well as improving your environmental sustainability.
Produce energy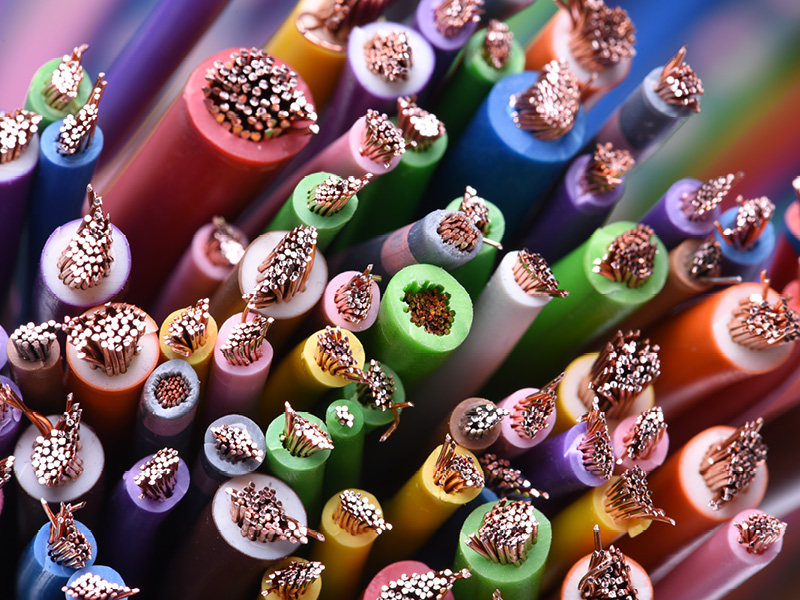
Increasingly businesses of all sizes are finding it more viable to find ways to generate their own power, covering all or part of the energy requirements of their operation.
Currently this is often in the form of photovoltaic (solar) production which can be combined with battery storage to manage the power production to align with the peak consumption.
During daylight hours, facilities can use their photovoltaic production to store energy in batteries (think Tesla Powerwall) which can then be used to offset high cost peak period consumption.
Alternative on site energy generation, such as biogas, can also help deal with the peaks in demand.
The world sources around 10 per cent of its energy needs from biomass. Following government policy shifts such as the Clean Technology Investment Program, many industrial sites that use biological wastewater treatment lagoons have installed covered anaerobic lagoon (CAL) systems.
These CAL systems are targeting more efficient effluent treatment methods that both reduce emissions and capture biogas as an on-site renewable energy source.
Although these systems won’t provide enough power to make food processing sites self-sustaining, the energy the CAL system can produce is enormous.
For example, one of Wiley’s recent projects at a rendering plant is currently generating half a megawatt of power each day, which is all used back in the processing plant.
Food facilities may also find elements of their supply can come from interesting sources.
Heat or steam recovery systems can take waste energy and return it to the operation as power.
In the process of sterilisation in food facilities, often our businesses heat water or produce steam to use for practical purposes.
Once the hot water has been used for its designated purpose, we can recover the thermal energy, thus minimising mainstream energy supplies such as those from gas or coal fired boilers.
Utilisation of heat pumps, which use energy from geothermal sources and recovered waste heat, is becoming more common too.
Manage energy
The best way to manage your energy is to monitor your use and mitigate spikes by implementing automated systems that optimise your consumption.
Having systems to help mitigate consumption can provide big savings. Examples include automated systems that prevent turning all power-hungry equipment on at the same time, matching equipment operating conditions to production, or providing variable plant control.
Managing consumption isn’t just about the draw from the grid, it’s also how we manage and conserve the impact that power provides, such as through the use of highly insulated facilities.
Also, depending on suppliers and billing agreements, there is an opportunity to save a significant amount of energy and cost by applying power factor correction and load balancing.
When considering the coupling of batteries with renewable energy, the opportunity exists to significantly decrease electrical consumption and cost for manufacturers.
This general premise would work on three principles:
- Using grid electricity during off-peak periods to run operations
- Using renewable energy to charge the batteries in off-peak periods
- Using the batteries during peak periods to assist in running operations
Preliminary calculations suggest that this reduction in peak demand could have the potential to save manufacturers up to 30 per cent on their monthly electricity costs.
In addition to batteries, there are other types of energy storage solutions that can assist in managing peak demand such as biogas that can be held under a pond cover and thermal energy that can be stored in the forms of insulated hot water tanks or even ice.
It is no secret that electricity costs will continue to rise due to necessary infrastructure investment.
As this continues, manufacturers will look at new ways to save energy and less costly alternatives to electricity from the supply grid.
Scott Hebbard is a senior process engineer at Wiley, which design builds and maintains facilities. Contact Scott on connect@wiley.com.au